Shaft Education: What goes into making a graphite shaft?
- Share on Facebook
- Share on Twitter
- Share by Email
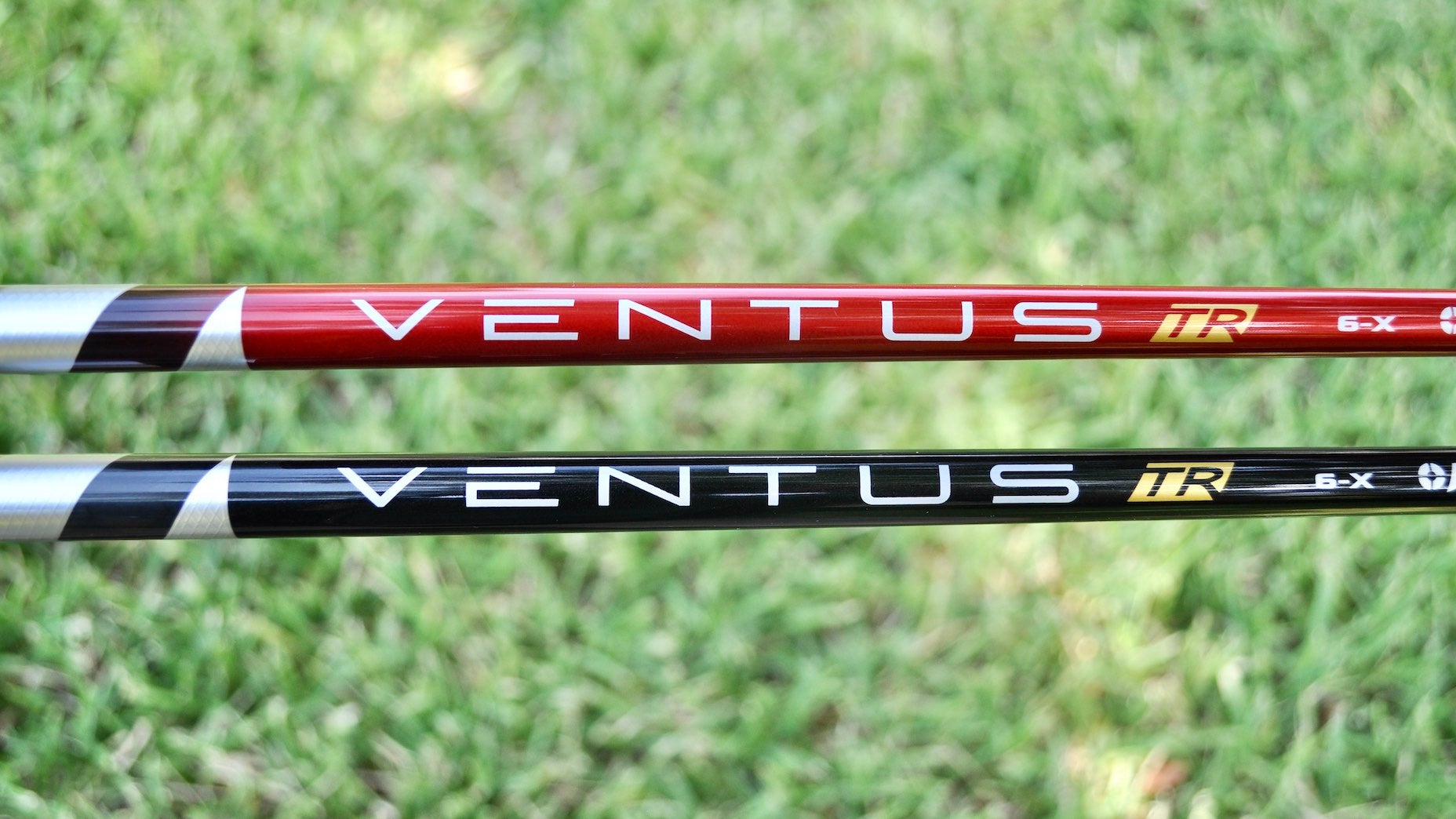
Ventus TR Red and Black feature similar materials but two wildly different profiles.
Jonathan Wall/GOLF
Golf equipment is downright mysterious. Aside from what we can see on the outside of our drivers, woods, irons, wedges and putters, rarely if ever do we get the chance to peek under the hood and see what kind of technology is hidden underneath.
This is especially true with composite shaft technology — so much of what we hear and know about how they’re constructed is obscured by fancy terminology, ratings and weight measurements.
Suffice it to say, composite shafts are intricate and complexly designed and constructed. And while we don’t have enough time (or expertise) to delve deep into all that carbon technology possesses, with help from Fujikura Composites, we can give you a bird’s-eye view of how shafts are made.
Golf shafts have carbon in them, but they’re actually composites
Wait, isn’t carbon and composite the same thing? Nope. Carbon is a chemical element that you can find on a periodic table. A composite is two or more materials comprised together. This means a “graphite shaft” is actually a composite shaft made of carbon fibers fused with resin/epoxy.
According to Fujikura’s online Shaft University, the technical term is Carbon Fiber, Reinforced Plastic (CFRP for short).
But wait, there’s more.
According to Fujikura, “Graphite is pure carbon with atoms that are arranged in a particular hexagonal-ring pattern. A polymer is a connected chain of carbon atoms. Carbon fibers are what the polymer becomes once it is stretched and oxidized. You can think of polymers as a bunch of graphite atoms standing next to each other.”
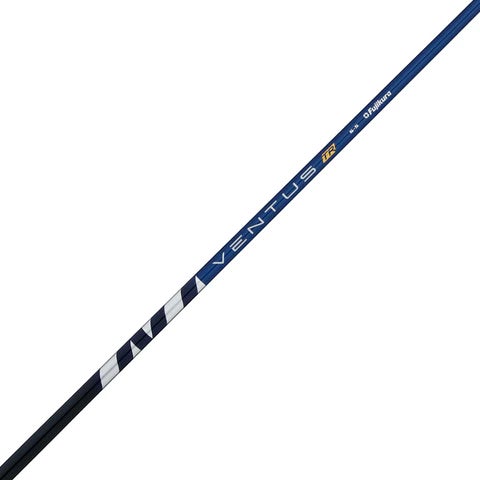
Fujikura Ventus TR Blue
What is pre-preg?
For those of you who actually read shaft technical descriptions, you’ve probably seen the word “pre-preg” before. But what is it? Pre-preg refers to sheets of carbon fiber that have previously (pre) been impregnated (preg) with resin to form a composite.
When you see a shaft labeled “low resin” or “max carbon”, that refers to the ratio of carbon and resin. Typically, the lower the resin amount, the lighter and more resilient the shaft is.
Then what?
Carbon fiber and resin composites are formed into a thin sheet of material. Depending on shaft model, type, flex, rating, etc., the shaft is rolled around a mandrel and fused together with resin to form a cylindrical shape.
Where things get complex is in the type of fibers used and how they’re oriented around the mandrel. There are different fiber types, patterns and orientations the sheets are rolled around the mandrel which affects feel and performance.
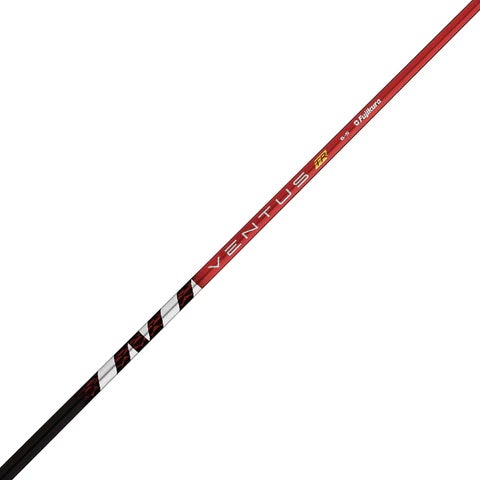
Fujikura Ventus TR Red
According to Fujikura, “[t]here are specific ‘clocking’ locations labeled on the mandrel that correspond with the layout on the design sheet. These clocking locations specify when and where the materials are to be applied and serve to balance materials as they are rolled to ensure a uniform shape.”
This step is crucial but becomes even more so as the number of plies increases. Each additional ply increases the complexity of the process.
How does the composite go from a flat sheet to a golf shaft?
Once the raw materials are created (the sheets of flexible composite material), it’s time to form the shaft. Shaft manufacturers, specifically Fujikura, use what’s called a design sheet that functions as a blueprint for how the shaft is to be rolled out on the mandrel.
On the design sheet is the amount of layers (also referred to as plies) of material required for each shaft, the desired orientation for each sheet as well as what order they should be applied. Cuts are made on a CNC machine, and each sheet is then hand-rolled (you read that correctly) around the mandrel. Some shafts may have 5-7 plies of material —others may have upwards of 20 or more. It all depends on what model is being built.
Once rolled, the composite sheet materials are fused together via extreme pressure and wrapped in cellophane for heat curing. The cellophane is then removed and the shaft is then sanded, washed and dried.
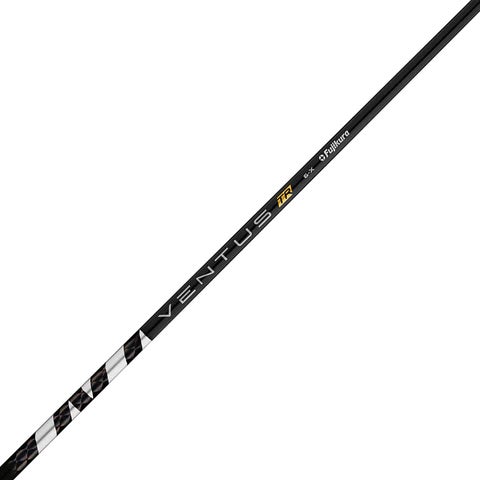
Fujikura Ventus TR Black
Fujikura takes it even further, offering its outermost layer of carbon fiber as a “sacrificial ply”, meaning it’s used as a protective layer and not for performance. Once done, it’s painted and finished for delivery direct to the consumer and/or an OEM.
At Fujikura, the next step in manufacturing a shaft is to paint it, but the company doesn’t just slap a coat of poly on top and call it good. Instead, Fujikura uses a specially designed finish called Phantium that is ultra-lightweight and saves 5-7 grams of weight when compared to traditionally used paints. And the lighter the paint, the more total weight Fujikura can control to ensure the shaft delivers maximum performance.
Quality control is serious business.
Once the shaft is rolled, cured, finished and painted, the fun begins. Each shaft at Fujikura is checked to ensure that not only are there no imperfections or blemishes, but also so that it demonstrates the exact bend profile and performance that it’s supposed to.
There’s way more to it than that
Shaft manufacturing is actually a much more complicated process than the one we’ve outlined above. For an in-depth look behind the curtain, Fujikura’s Shaft University is one of the best resources on the net about the subject.
Latest In Gear
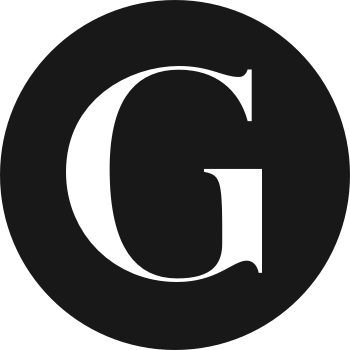
Ryan Noll
Golf.com Contributor