Wild story reveals how far golf-ball manufacturing standards have come
- Share on Facebook
- Share on Twitter
- Share by Email
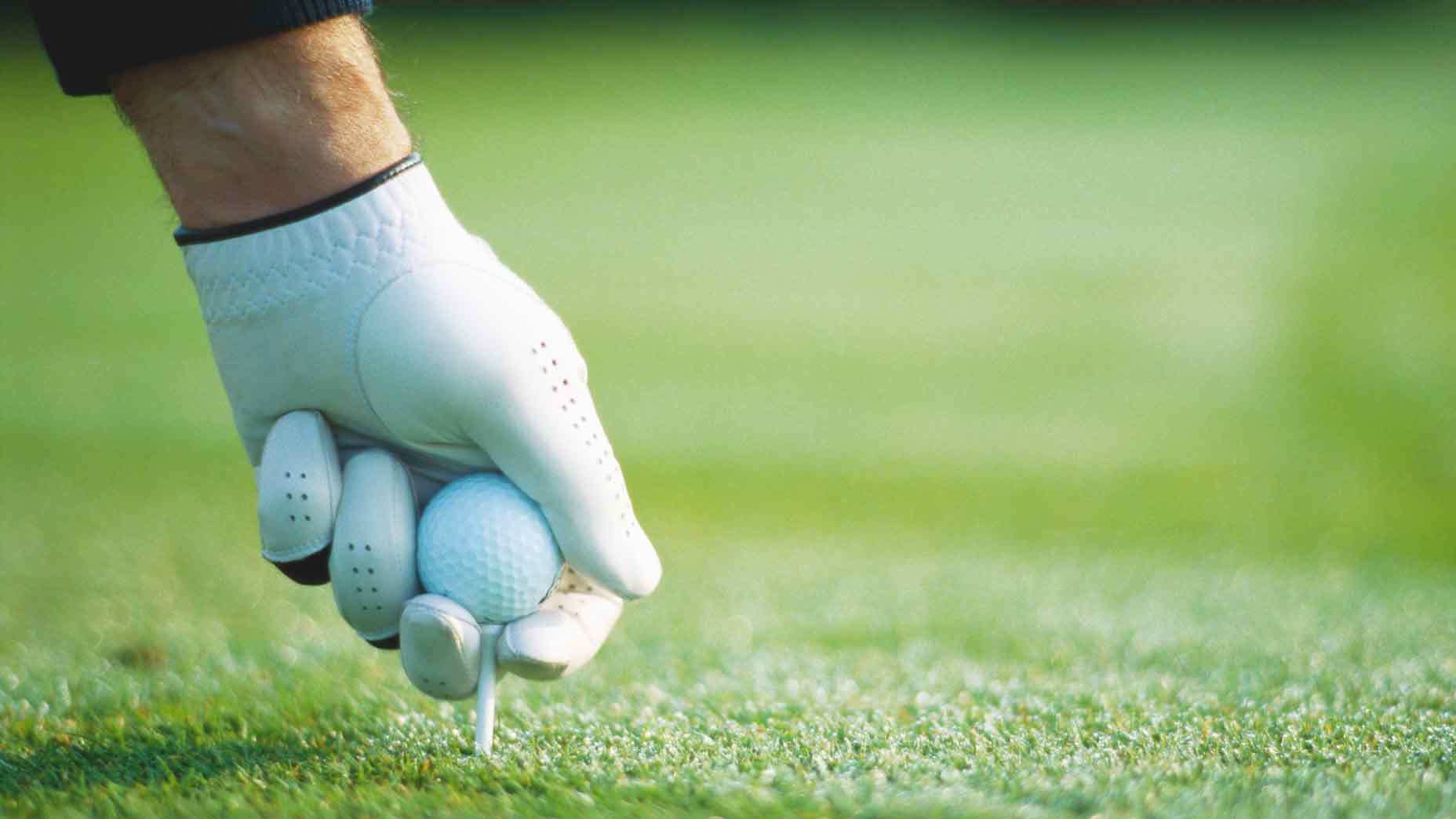
Not all golf balls were created equal years ago.
Getty Images
Pick up a dozen golf balls from your favorite manufacturer and you can rest easy knowing the dozen pellets packed inside are practically identical from one to the next. Thanks to tighter manufacturing tolerances and improved processes — not to mention better materials — there’s very little deviation in performance.
It’s part of the creation process that tends to get overlooked when golfers are seeking out a piece of gear, which is understandable. Knowing how the sausage is made isn’t nearly as exciting as determining if the ball in your hand is going to help you shoot lower scores. Most golfers tend to assume all balls are made the same, which isn’t the case.
There are plenty of machines and people, for that matter, behind the scenes ensuring the manufacturing process goes smoothly.
If you don’t believe me, check out Titleist’s ball plant in New Bedford, Mass., or Callaway’s in Chicopee, Mass., to gain a better appreciation for the manufacturing process.
Robot testing every 2023 golf ball: Here’s the best option for YOUR gameBy: Jonathan Wall
If you’re wondering why we keep harping on manufacturing tolerances and processes, it’s because they’ve come a long way over the decades — and that’s a good thing.
During the latest episode of GOLF’s Fully Equipped podcast, co-host Gene Parente shared the story of how Spalding Golf used to hand-pick the best golf balls for its stable of pros. Tolerances were noticeably looser across most of the industry decades ago, which meant golf ball performance could vary wildly from one ball to the next with some manufacturers.
“Manufacturing tolerances weren’t nearly as tight for golf balls [as they are today],” Parente said. “So [Spalding] had a robot down in Palm Desert — in the Palm Springs area — an old Iron Byron, and they told me they’d take 500 golf balls or 750 golf balls, at 110 mph, and they’d go out and take the balls that were plus or minus 30 yards greater right and left and discard them.

TaylorMade TP5x pix USA Golf Balls
$49.99
View Product
“They’d do this five times until they got down to x number of dozens of golf balls that they knew went straight from a quality control standpoint — and those were the balls that went to the Tour. There’s a clear example of how they knew what their manufacturing tolerance was. All these balls were conforming, but the average [golfer] had no idea they were playing a ball that was doing that. Those stories are long gone because the quality control on golf balls has really improved on golf balls. It’s not necessary like it used to be.”
The last sentence perfectly sums up how far manufacturing has come since Spalding culled through their golf balls to select the best pellets for their pros. Nowadays, the ball in your bag is manufactured in the same way as the one in Jordan Spieth’s bag or Rory McIlroy’s bag, removing the need to give the pros an edge over the weekend golfer in the quality department.
But times were different back then. The story is a good reminder of how equipment and manufacturing tolerances have changed for the better for pros and amateurs alike.
Want to overhaul your bag for 2023? Find a fitting location near you at True Spec Golf.
Latest In Gear
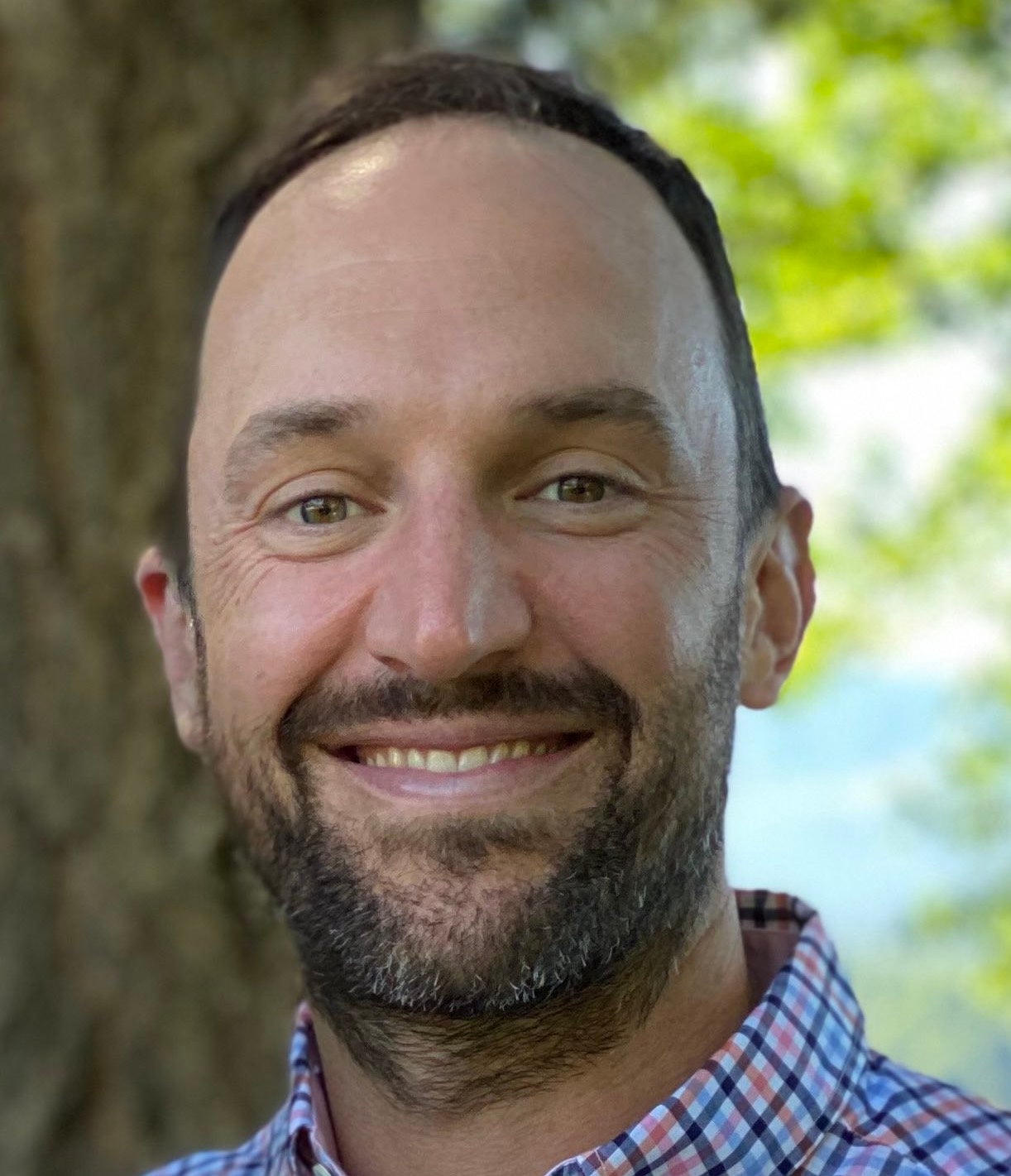
Jonathan Wall
Golf.com Editor
Jonathan Wall is GOLF Magazine and GOLF.com’s Managing Editor for Equipment. Prior to joining the staff at the end of 2018, he spent 6 years covering equipment for the PGA Tour. He can be reached at jonathan.wall@golf.com.